Have a Good Day with Finning
Happy is a day when things go right. When the wheels turn, the engines roar and the work gets done.
Taking advantage of on-board tech to enhance operator skills
The state of a machine’s undercarriage can significantly impact performance. A well cared for undercarriage will help to maximise power, increase safety and stability and will keep operational repair costs to a minimum over a machine’s lifecycle.
A daily walk around a machine is a simple but very effective way for operators to identify any obvious issues or damage to the undercarriage. Not doing this can cost you – both in terms of any repairs needed – not to mention the costs associated with machine downtime.
Regularly checking your undercarriage will also enable you to get a clearer view on what worn looks like. The rate of wear, very much depends on the environment the machine is working in. For example, a machine operating in a quarry to excavate granite is putting a great deal of strain on the machine. While other materials such as clay or sand can increase the track tension when solidified.
Certain operational movements can also increase the level of undercarriage damage. These include, for example, making sharp turns, excessive reversing or driving at high speeds. In addition, not having the track tension correctly adjusted can also cause damage over time as will the build-up of dirt and debris causing tracks to stretch and then ultimately break.
Cleaning the tracks thoroughly, particularly in wintery conditions, is also essential to avoid materials drying or freezing on the undercarriage overnight. Scheduling regular maintenance sessions alongside frequent daily spot checks will reduce the risk of damage and more costly repairs down the line as well as reduced productivity.
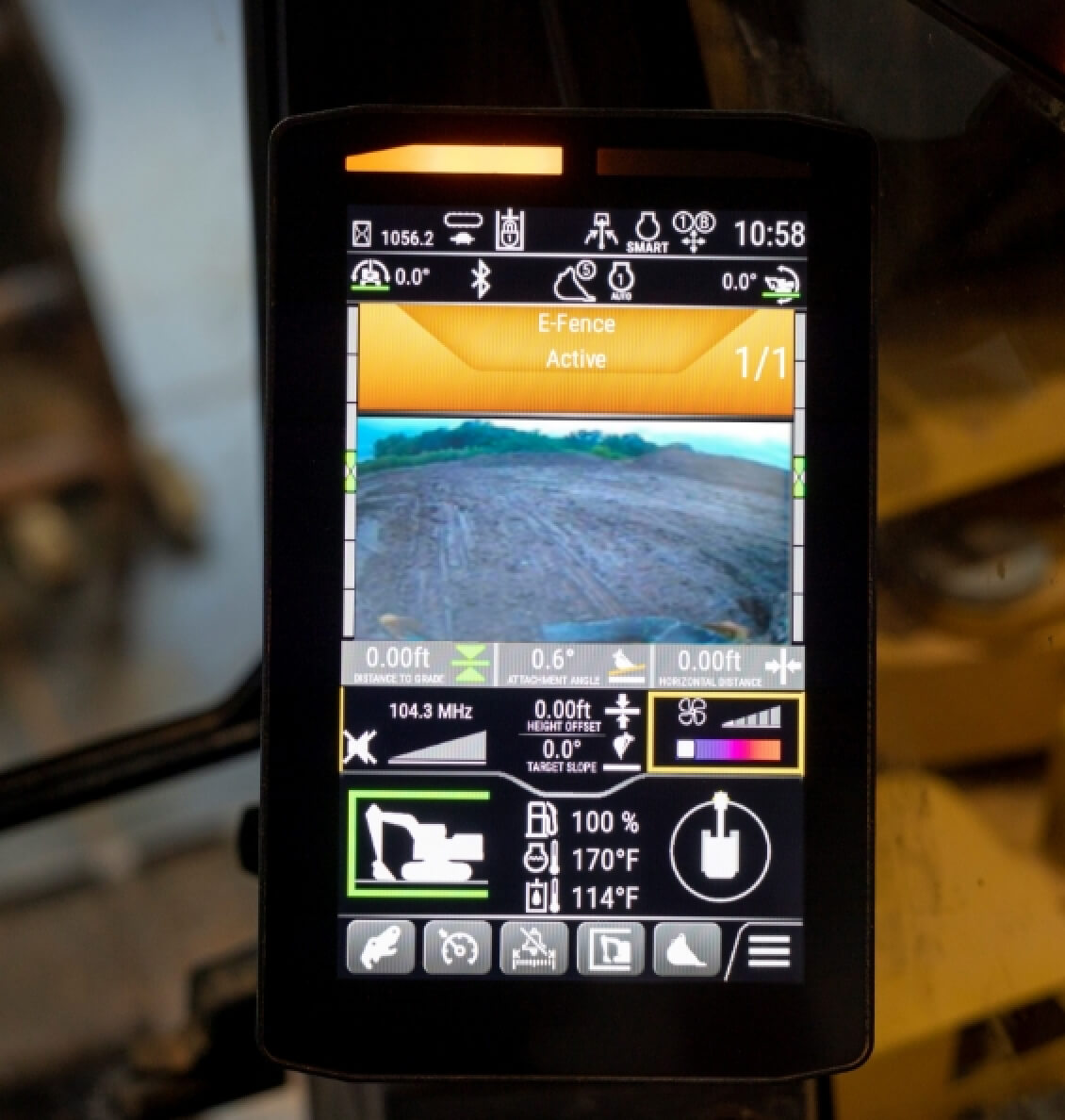
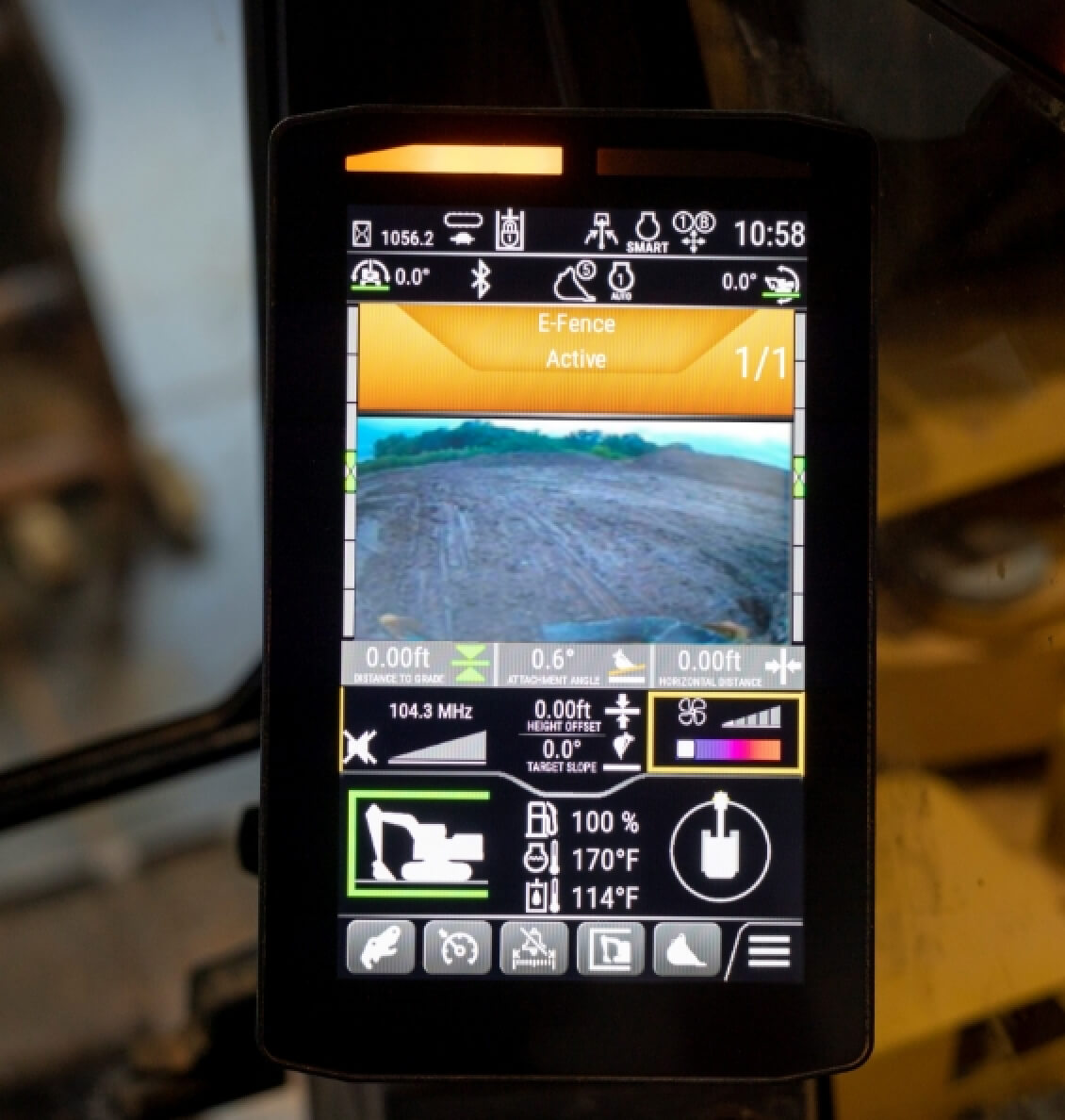
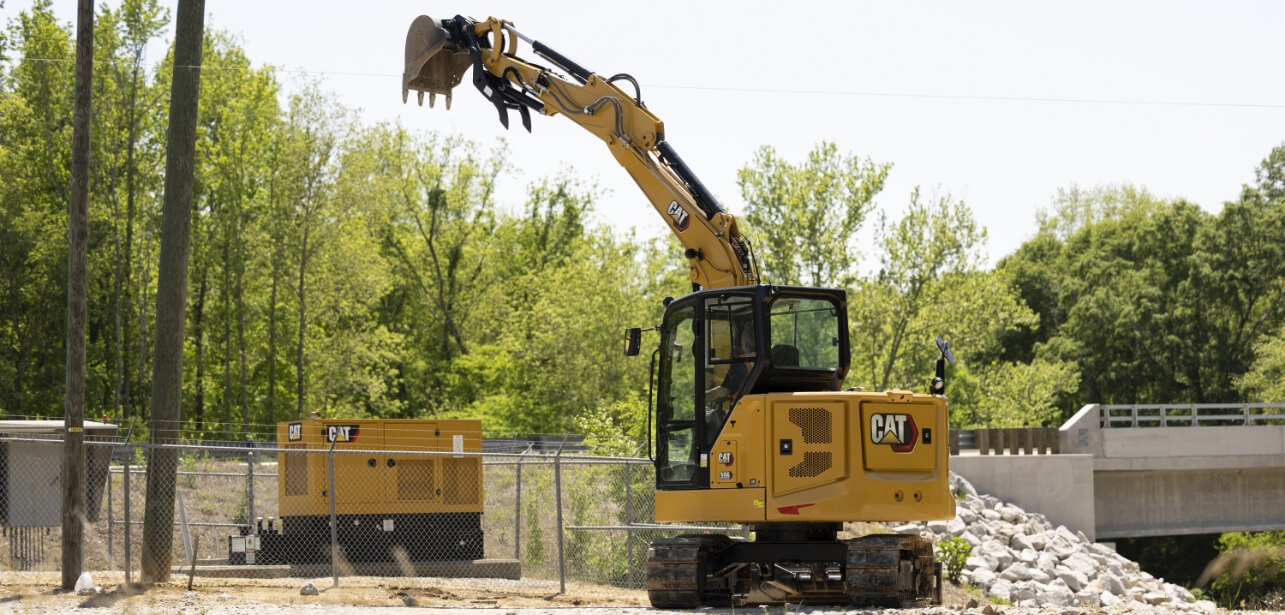
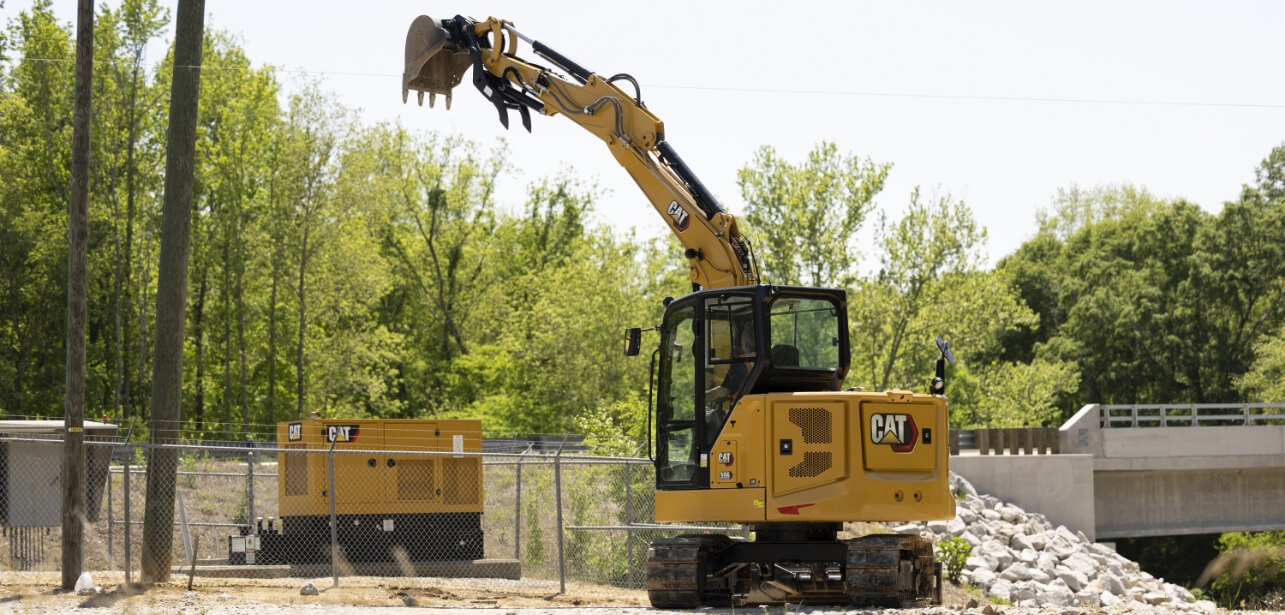
Indicate
Training on the system is crucial to get the most out of the features and fully utilise its potential. In addition, using Indicate on groundworks improves accuracy, reduces operator fatigue (from not over cutting, over swinging and reworking) and is much safer for those on site, as it significantly reduces the need for on-the-ground grade checking.
e-fence
Swing assist
Bucket Assist
Training for optimum use and value
Used in combination, these features can significantly reduce the day-to-day operating costs of a machine and impact the total cost of ownership. The features give the operator a helping hand enabling them to utilise the full capabilities of the equipment so they can run it to an optimum level across a range of onsite tasks, which leads to better fuel efficiency, reduced downtime and longer lifespan of the machine.
But training is really the key factor. A large proportion of operators just don’t make use of them and take advantage of the operational benefits they offer. Having a good understanding of what the features are and how to use the controls effectively to get the most out of a machine is so important and can enable operators to complete tasks more quickly and effectively.
As standard Finning UK & Ireland provides a full overview of the built-in technology features when handing over new equipment to customers. We’ve also developed a series of short instruction videos that are available on YouTube to show step-by-step how the features work and how operators can get the most out of them.
Check them out here: https://www.youtube.com/playlist?list=PLm8lTgDqLtG09MsodrXCscHlhzvgrfNY1
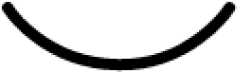
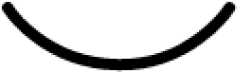